What are PVD (Physical Vapor Deposition) Coatings?
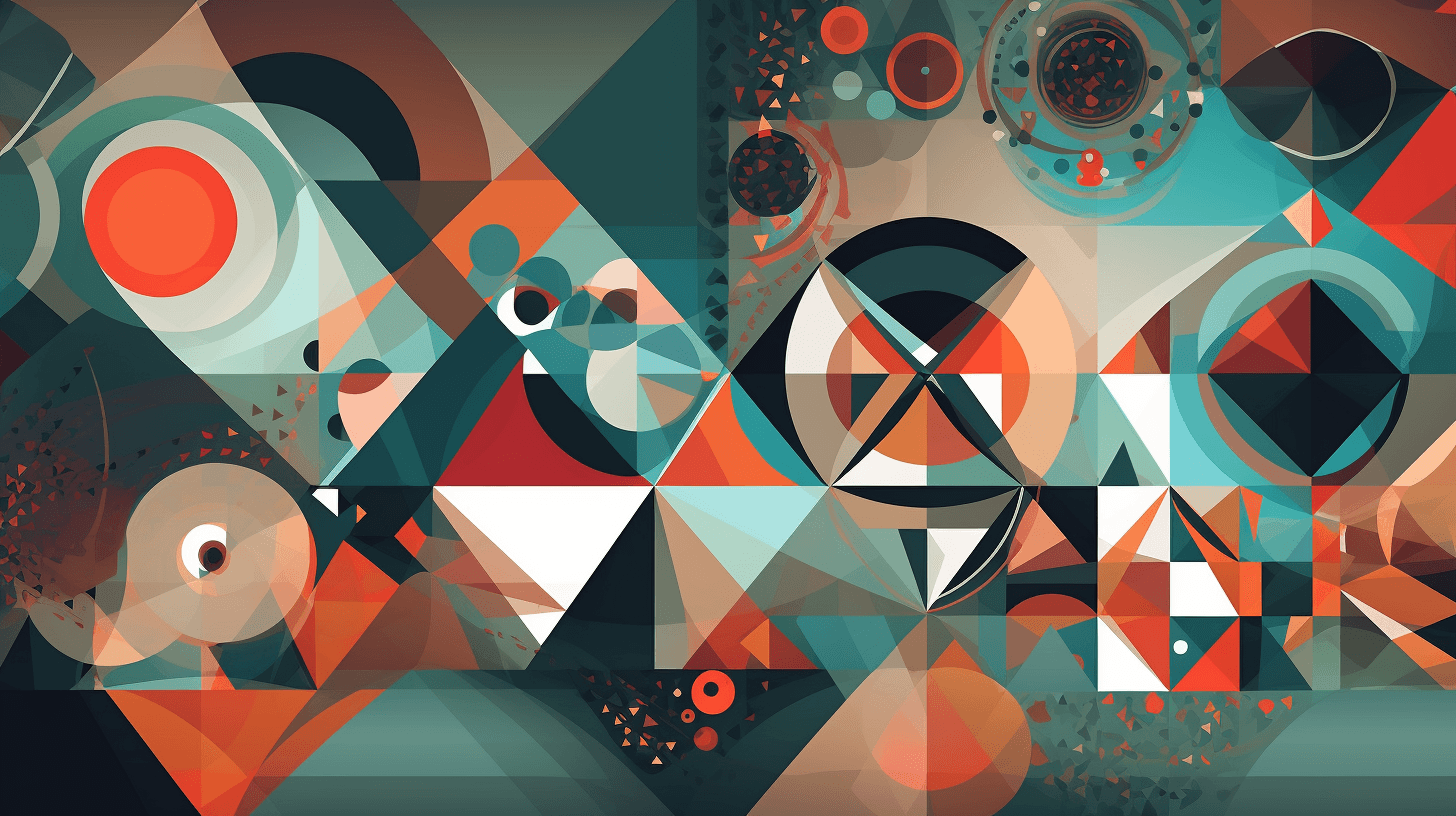
In today's competitive market, selecting the right coating solution is crucial for various industries. One advanced technique that has gained popularity for its ability to improve durability, wear resistance, and overall performance of materials is PVD (Physical Vapor Deposition) coating. In this article, we'll dive deep into PVD coating, exploring its benefits, applications, and how it compares to other popular coating techniques.
Whether you're a professional looking to make an informed purchase decision or simply curious about PVD coatings, this article aims to provide valuable insights that will help you understand the importance of PVD coating and how it can solve various problems in different industries.
What is PVD Coating?
PVD coating is a vacuum-based process that involves the deposition of thin layers of materials onto various substrates. This technique is used to enhance the properties of the substrate, such as wear resistance, hardness, and corrosion protection. There are several types of PVD processes, but the most common ones include sputtering and evaporation.
Sputtering
In the realm of thin-film deposition technologies, sputtering deposition stands out as a versatile and powerful technique. Enabling the creation of high-quality, uniform films, sputtering deposition plays a crucial role in numerous industries, enhancing the performance, longevity, and aesthetic appeal of various products.
Sputtering deposition is a physical vapor deposition (PVD) process that allows the coating of complex surfaces with a wide array of materials. During the application, atoms are ejected from a solid target material due to bombardment of the target by energetic particles From the computer chips powering our digital world, the solar cells harnessing the sun's energy, to the optical coatings improving our vision technologies, the impact of sputtering deposition is profound and pervasive.
The Sputtering Process
The process begins with ion bombardment, where ions from an ionized gas collide with a target material. This collision causes atoms from the target to be ejected. These ejected atoms then travel through the vacuum environment to deposit onto a substrate, forming a thin film.
Types of Sputtering
Sputtering can be achieved through various methods, each with unique benefits:
- DC Sputtering: Direct current sputtering is used with conductive target materials.
- RF Sputtering: Radio frequency sputtering is used with insulating target materials.
- Magnetron Sputtering: Enhances the efficiency of the sputtering process using a magnetic field.
- Reactive Sputtering: Introduces reactive gases into the chamber to form compound materials on the substrate.
Properties of Sputtering Coatings
Sputtering coatings are known for their:
- Adhesion: Excellent bonding with the substrate.
- Uniformity: High degree of thickness uniformity across the substrate.
- Quality: Ability to form high-quality films with precise control over the film properties.
Advantages of Sputtering Deposition
Sputtering deposition provides several advantages, including:
- High Precision and Control: The ability to control the deposition rate allows for high precision films.
- Excellent Adhesion and Uniformity: Sputtered films exhibit excellent adhesion to the substrate and uniformity across complex shapes.
- Ability to Coat Complex Geometries: The process can evenly coat complex and non-planar surfaces.
Applications of Sputtering Deposition
Sputtering deposition is used in various industries:
- Electronics and Semiconductor Industry: Used for the deposition of thin films in the manufacturing of integrated circuits and other electronic components.
- Solar Cells Industry: Used in the production of thin-film solar cells.
- Optical Components: Used to create anti-reflective coatings and other optical films.
- Decorative and Functional Coatings: Used to enhance aesthetic and functional properties of various products.
Evaporation
In evaporation, the coating material is heated until it vaporizes and then deposited onto the substrate.
Benefits and Advantages of PVD Coating
PVD coatings offer numerous benefits, including:
- Improved wear resistance
- Enhanced corrosion protection
- Increased hardness
- Reduced friction
- Attractive surface appearance
These benefits translate into improved product performance, longer lifespans, and reduced maintenance costs.
Common Applications of PVD Coating
PVD coatings are used in a wide range of industries, such as:
- Aerospace
- Automotive
- Electronics
- Medical
Examples of products and components that benefit from PVD coatings include cutting tools, engine components, electronic devices, and medical implants.
PVD Coating Process
The PVD coating process generally involves the following steps:
- Surface preparation: Cleaning and preparing the substrate for coating
- Deposition: Applying the coating material using sputtering or evaporation techniques
- Post-treatment: Cooling and/or annealing the coated substrate to achieve desired properties
Controlling process parameters, such as temperature, pressure, and deposition rate, is essential for achieving the desired coating properties and performance.
Types of PVD Coating Materials
Various materials can be used for PVD coatings, including metals, alloys, and ceramics. The choice of coating material affects the coating's properties and performance. For example, a titanium nitride (TiN) coating provides excellent wear resistance, while a chromium nitride (CrN) coating offers enhanced corrosion protection.
Comparing PVD with Other Coating Techniques
PVD coating can be compared to other popular coating methods, such as CVD (Chemical Vapor Deposition) and electroplating. Each method has its own set of advantages and disadvantages, depending on the specific application.
- PVD: Offers excellent wear resistance, thin and uniform coatings, and a wide range of coating materials. However, it may be more expensive and slower compared to other methods.
- CVD: Allows for the deposition of very thin and conformal coatings, but may involve higher temperatures and potentially hazardous chemicals.
- Electroplating: Provides a relatively low-cost and fast method for applying coatings, but may not achieve the same level of wear resistance and uniformity as PVD coatings.
Conclusion
In this article, we explored the world of PVD coatings, discussing their benefits, applications, and comparison with other popular coating techniques. PVD coating plays a crucial role in improving the performance and longevity of various materials and components across numerous industries, such as aerospace, automotive, electronics, and medical.
The advantages of PVD coating, including wear resistance, corrosion protection, and hardness, make it an attractive option for many applications. However, it's essential to consider other coating methods, such as CVD and electroplating, depending on the specific requirements of your project.
As someone researching a purchase decision or seeking to deepen their understanding of coating solutions, we hope this article has provided valuable insights to help you make an informed choice. We encourage you to explore further resources and continue expanding your knowledge in the field of coatings, as it's a constantly evolving area with potential for future growth and innovation.