Heat Treating: A Comprehensive Guide to Enhancing Material Properties
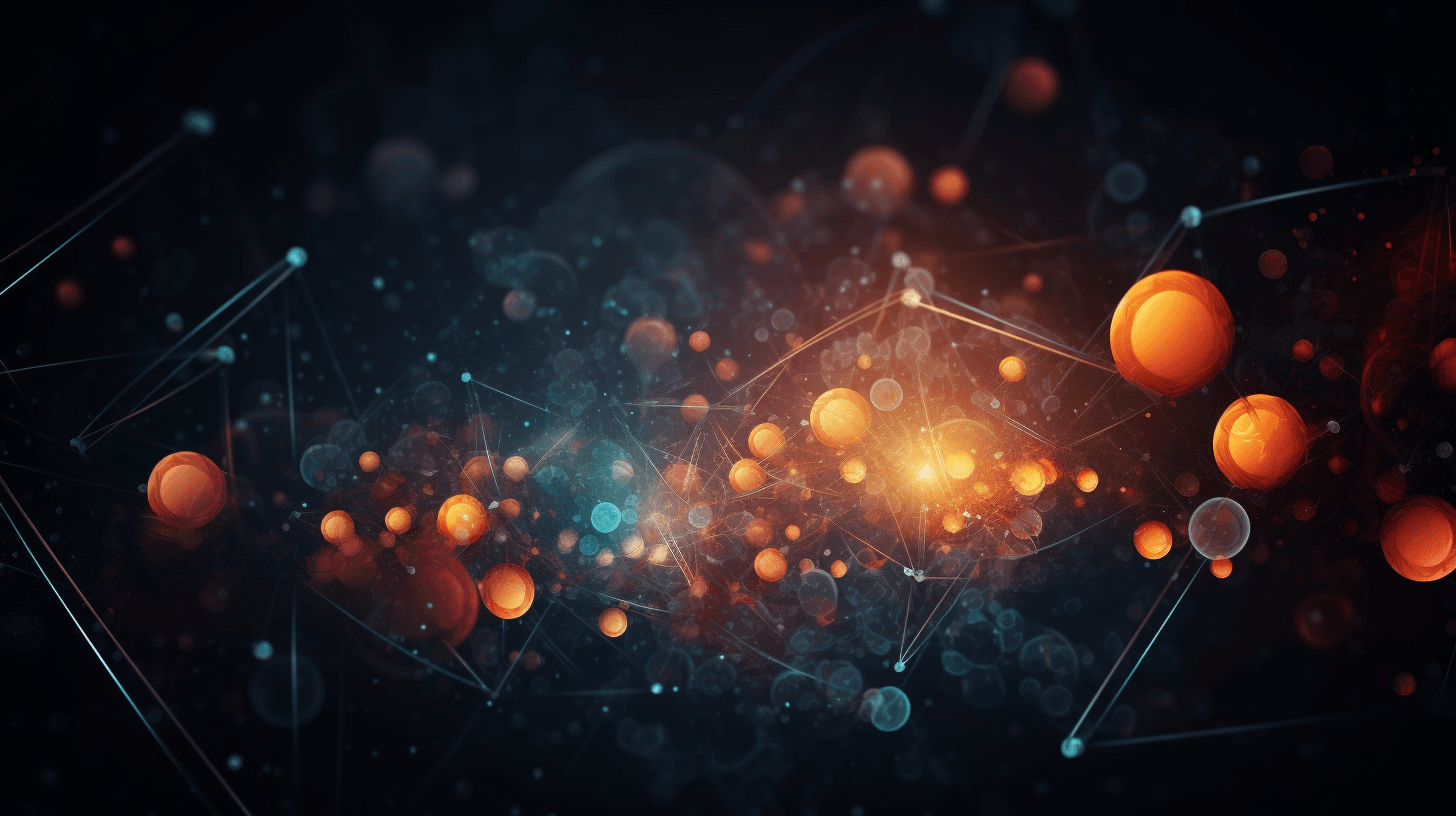
Heat treating is a critical process in altering the physical and mechanical properties of materials, primarily metals and alloys. By controlling the heating and cooling of materials, heat treating allows engineers and manufacturers to tailor specific properties to meet the demands of various applications. In this article, we will provide a comprehensive guide to understanding heat treating, its benefits, applications, types of processes, factors affecting the outcome, and the equipment and techniques used in the industry.
Whether you're a professional researching purchase decisions or simply looking to expand your knowledge of heat treating, this guide aims to provide valuable insights into the importance of heat treating and its potential applications across a range of industries.
What is Heat Treating?
Heat treating is a critical process that involves heating and cooling materials, primarily metals and alloys, to alter their physical and mechanical properties. This process is essential in various industries, as it allows engineers and manufacturers to tailor specific properties to meet the demands of diverse applications.
Benefits of Heat Treating
Heat treating offers numerous benefits, such as:
- Improved strength
- Enhanced hardness
- Increased ductility
- Greater resistance to wear and corrosion
These benefits result in enhanced performance and extended service life of the treated components.
Common Applications of Heat Treating
Heat treating is commonly used in a variety of industries, including:
- Automotive
- Aerospace
- Tool manufacturing
Examples of components that benefit from heat treating include gears, engine parts, cutting tools, and aerospace components.
Types of Heat Treating Processes
There are several types of heat treating processes, each serving a specific purpose:
Annealing
A process that involves heating a material to a specific temperature, holding it there for a period of time, and then cooling it slowly to achieve a more uniform and softer microstructure.
Quenching
A process in which a material is rapidly cooled from a high temperature, typically by immersion in water, oil, or another cooling medium, to increase its hardness and strength.
Tempering
A process that involves heating a previously quenched material to a specific temperature and then cooling it to achieve a balance between hardness and ductility.
Normalizing
A process similar to annealing, where a material is heated to a specific temperature and then cooled in air to achieve a more uniform microstructure and improved mechanical properties.
Factors Affecting Heat Treating
Several critical factors affect the outcome of heat treating processes:
- Temperature
- Time
- Cooling rate
- Material composition
Controlling these factors is crucial for achieving the desired results and properties in treated components.
Heat Treating Equipment and Techniques
Various types of heat treating equipment and techniques are available, including:
- Furnaces (e.g., batch and continuous)
- Ovens
- Induction heating systems
Each method has its advantages and disadvantages, depending on the specific requirements of the application.
Furnaces
Batch and continuous furnaces are commonly used for heat treating processes. Batch furnaces are suited for smaller production volumes, while continuous furnaces can handle larger volumes and offer better temperature uniformity.
Ovens
Ovens are often used for lower temperature heat treating processes, such as tempering and stress relieving, and provide excellent temperature control and uniformity.
Induction Heating Systems
Induction heating systems utilize electromagnetic fields to generate heat within the material. This method offers rapid heating rates and precise temperature control but may require specialized equipment and be more expensive.
Quality Control and Inspection in Heat Treating
Quality control and inspection are essential in heat treating processes to ensure the desired properties are achieved. Common inspection methods include:
- Hardness testing
- Microstructure examination
- Non-destructive testing (e.g., ultrasonic, magnetic particle, and dye penetrant testing)
These inspection methods help identify potential defects or deviations from the required properties, ensuring the treated components meet the necessary performance standards.